Choosing the Right Wear-Resistant Material for Your Industry Needs
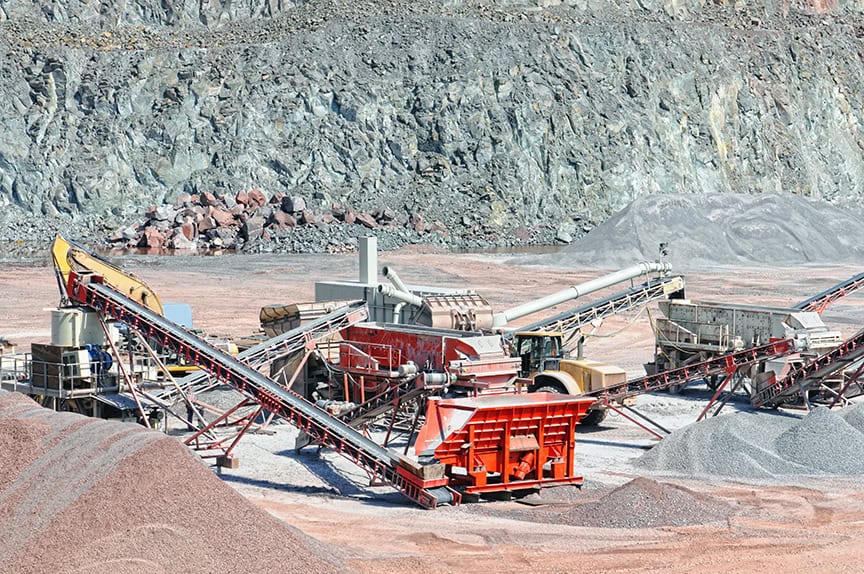
In industries like mining, aggregate, and construction, equipment doesn’t just work hard—it takes a beating. Constant exposure to abrasion and corrosive elements—think of the environment in cement plants—can lead to excessive wear, costly downtime, and frequent repairs. That’s where wear-resistant materials play a crucial role. Selecting the right wear-resistant material isn’t just about protecting […]
The Future of Composites in Construction: Innovations to Watch
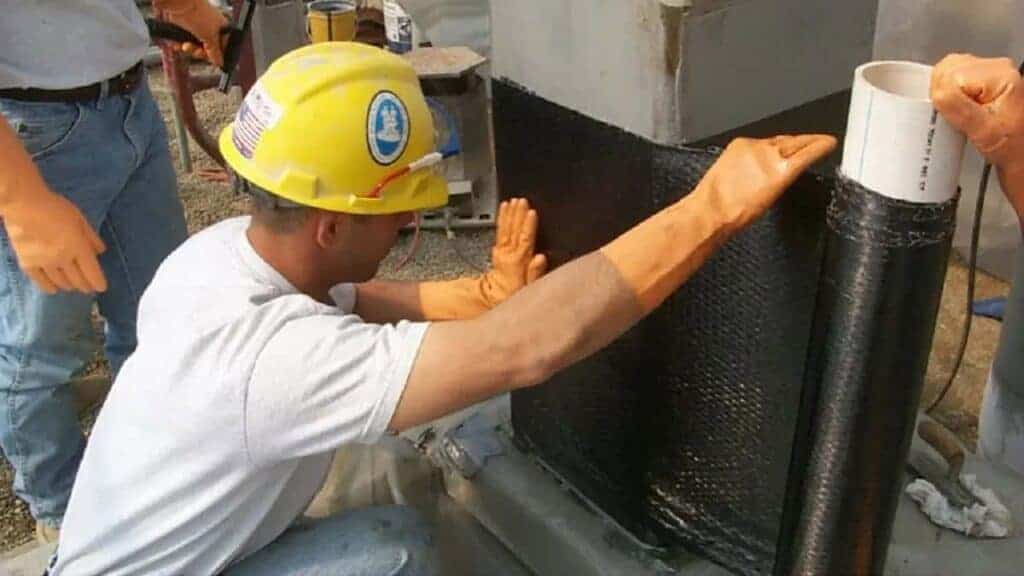
The construction industry is evolving, but when it comes to composites, innovation isn’t just about new materials—it’s also about better applications. While composites have been used in construction for decades, the industry continues to optimize their use for greater durability, efficiency, and sustainability. Composite solutions like structural reinforcement and pipe repair are helping extend the […]