Category Archive: Epoxy Coatings & Joint Filler
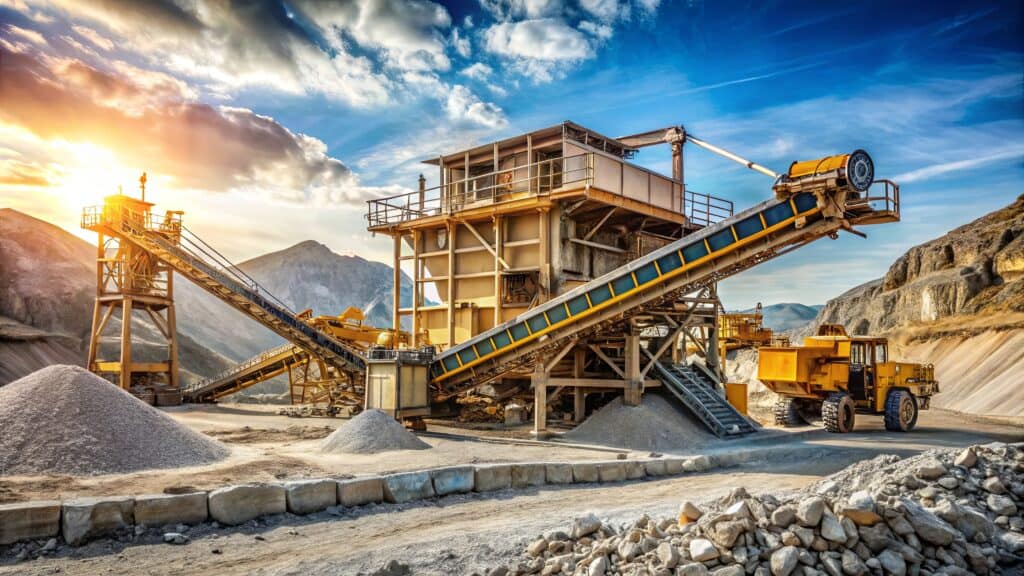
Mining and aggregate operations are some of the most punishing environments of any industry. From rock crushing to slurry movement, equipment is subject to constant impact, abrasion, and corrosion—all of which take a heavy toll on unprotected surfaces.
In these conditions, wear-resistant materials make all the difference in helping you maintain safety, uptime, and profitability. At Copps Industries, we formulate high-performance epoxy systems designed specifically to meet harsh conditions and tough challenges. Our solutions help you extend equipment life, reduce downtime, and lower your total cost of ownership.
Here are five of the most common—and critical—applications where our materials make a difference:
1. Crushers: Liner Backing for Maximum Protection
The Challenge: Crushers are the workhorses of many mining and aggregate operations, facing extreme forces as they break down large materials. Impact, compression, and vibration lead to liner wear, misalignment, and structural damage.
The Solution: Copps’ crusher backing compounds fill cavities behind wear parts and support liner surfaces, reducing movement and minimizing the effects of vibration and impact. Our systems help protect the integrity of crushers, reducing maintenance and unplanned shutdowns.
2. Chutes and Hoppers: Shielding Against Abrasion
The Challenge: Chutes and hoppers experience constant material flow, often at high velocities. Over time, this flow erodes surfaces and creates pits or grooves that lead to equipment failure.
The Solution: Copps offers epoxy wear liners that provide a durable, non-metallic barrier in high-impact zones. These materials are ideal for extending the life of steel and concrete components and can be applied by trowel or pour, depending on site needs.
3. Conveyors and Transfer Points: Keeping Material Moving
The Challenge: Conveyors and transfer points are under constant friction and impact, making them vulnerable to wear along skirting, beds, and loading zones. Unprotected components result in material loss, misalignment, and premature equipment failure.
The Solution: Our wear-resistant epoxy coatings protect these high-friction areas, reducing maintenance needs and preventing breakdowns. By improving surface integrity, we ensure smooth, reliable material transport throughout your operation.
4. Pumps and Cyclones: Combating Erosion in Slurry Systems
The Challenge: In systems handling abrasive slurries, high-velocity flows rapidly erode internal surfaces, compromising performance and increasing maintenance frequency.
The Solution: Copps’ repair and rebuild compounds are formulated for harsh, wet environments. They restore damaged surfaces and add a protective epoxy layer that resists erosion and chemical attack and extends service life.
5. Screening and Sorting Equipment: Preserving Efficiency
The Challenge: Screening and sorting machines are exposed to intense vibration and impact, which cause component failure over time.
The Solution: Copps’ grouts and coatings reinforce screen housings, frame joints, and mounting points. These products help prevent structural degradation, ensuring your systems remain efficient and accurate.
Innovation from Copps Industries
At Copps Industries, we develop purpose-built solutions that thrive under pressure. Our full line of crusher backing compounds delivers the performance you need in the most demanding environments:
- Cold cure crusher backing performs reliably in low-temperature environments (25°F to 60°F / -4°C to 16°C).
- Non-corrosive bushing lock is the industry standard for eccentric assemblies, preventing bushing rotation and extending equipment life.
Key Advantages of Copps Wear-Resistant Epoxies:
- Extended machinery life through better impact and vibration resistance
- Exceptional compressive strength and a broader array of service temperatures
- Low shrinkage to prevent voids and misalignments
- Elimination of wear liner gaps for better impact resistance
- Enhanced safety (no molten metals required, unlike traditional methods)
- ISO 9001-certified quality control for consistent performance
Extend Your Equipment Life, Improve Your ROI
In high-impact industries like mining and aggregate, wear-resistant materials aren’t optional—they’re essential. The right protection can mean the difference between unexpected downtime and uninterrupted production.
Copps Industries delivers proven solutions engineered to match the intensity of your operation. We help you get more out of your equipment, reduce your maintenance costs, and protect your bottom line. Explore our full line of epoxy systems for mining and aggregate applications, or contact us to discuss a custom formulation designed to meet your site’s specific challenges.
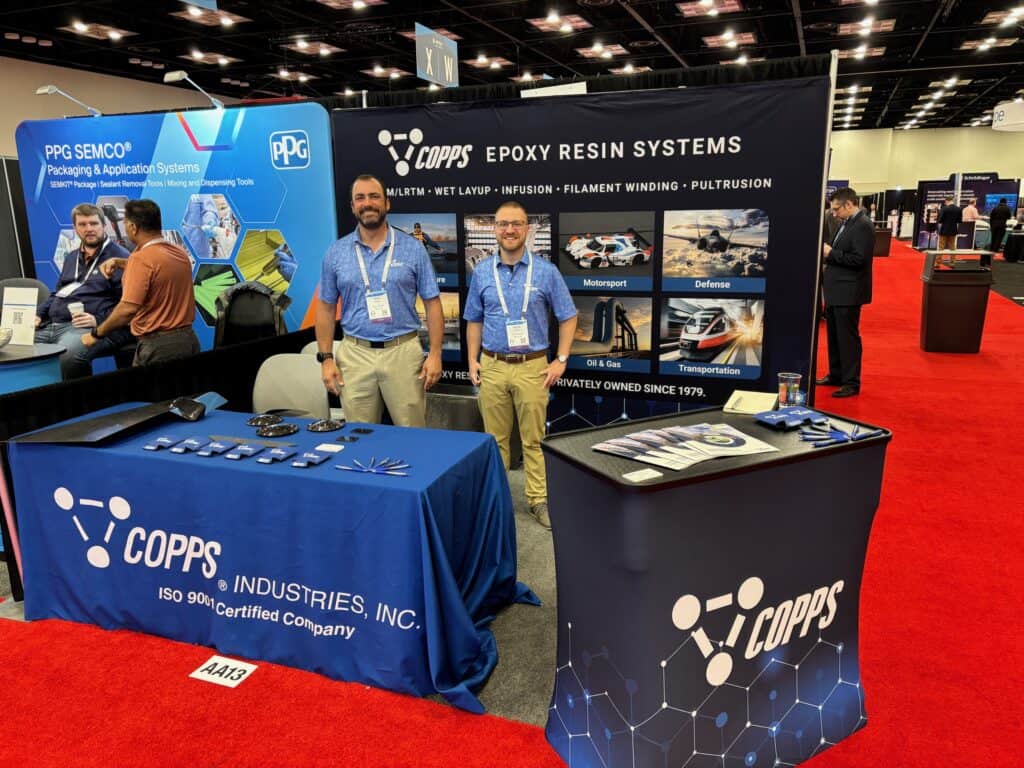
The SAMPE 2025 Annual Conference and Exhibition, held May 19–22 in Indianapolis, Indiana, brought together professionals across materials science and engineering for another year of cutting-edge innovation, knowledge sharing, and industry connection. Once again, SAMPE delivered a powerful mix of technical sessions, keynote presentations, hands-on workshops, and networking opportunities.
Copps Industries at SAMPE 2025
Copps Industries was proud to participate in this year’s conference, connecting with leaders in composites and advanced materials. We debuted our new and improved booth, showcasing our specialized epoxy solutions for a wide range of industrial markets—from mining to marine to aerospace. The exhibit hall buzzed with energy, offering valuable opportunities to engage with current and future partners and explore how our solutions can meet evolving industry needs.
Keynote: Pushing Boundaries—On Earth and Beyond
This year’s keynote address, “Beyond Gravity: Forging the Future in Space,” by Jennifer Buchli, NASA’s ISS Program Chief Scientist, offered an inspiring look at how materials innovation is shaping space exploration. Buchli detailed how experiments conducted aboard the International Space Station are redefining what’s possible in additive manufacturing, durability testing, and future materials—all with meaningful applications both in orbit and here on Earth.
Themes of Evolution and Next-Generation Solutions
The conference featured several sessions and panels reflecting key themes of advancement in the industry and next-generation solutions. Some of those sessions included:
- Toughness in Composites: Industry experts examined the challenge of toughness in fiber-reinforced composites. Presenters explored solutions like improved fiber-matrix adhesion, optimized orientation, and particulate additions—strategies that align with our own work at Copps in enhancing material durability and extending product lifespan.
- Digital Tools in Material Science: Tutorials on artificial intelligence and other digitalization techniques stood out as a future-focused highlight. Participants gained hands-on experience with AI-powered software and learned how digital tools are transforming the development, testing, and production of new materials to reduce trial and error and accelerate time-to-market.
- High-Performance in Automotive and Motorsports: Advanced materials for automotive and racing applications took center stage in panel discussions exploring lightweight composites, additive manufacturing, and the use of AI in material selection and design. For an added experience, attendees toured the Dallara IndyCar Factory and Purdue’s Sports Engineering Center, witnessing carbon fiber layups, autoclave curing, and real-world feedback systems in action.
- FAA Research on Next-Gen Materials: The FAA’s Joint Center of Excellence for Advanced Materials (JAMS) presented collaborative research on crashworthiness, durability, test methods, and more. Their work shone a spotlight on the importance of certification and standardization as advanced materials become more deeply integrated into transport systems.
More Than a Conference: Education, Innovation, and Connection
With over 200 exhibitors and 60+ product categories, the SAMPE 2025 Exhibit Hall remained a focal point of the event. Live demos, new product rollouts, and the exchange of ideas made the expo floor a dynamic place for insight and community.
In addition to technical sessions, SAMPE offered educational programming spanning ITAR-governed topics, sustainability, and process optimization. Networking events also gave attendees a chance to connect, ranging from student competitions to professional development sessions.
Copps Industries: Continuing the Conversation
Many of this year’s themes resonate with our mission at Copps. As a trusted supplier of epoxy solutions, we’re committed to helping customers meet today’s toughest challenges with products that perform, endure, and adapt.
We’re grateful for the opportunity to be part of the SAMPE 2025 experience and excited to apply what we’ve learned as we continue pushing the boundaries of materials innovation. Reach out and we’ll help you find the best solution to meet your needs in any industry.
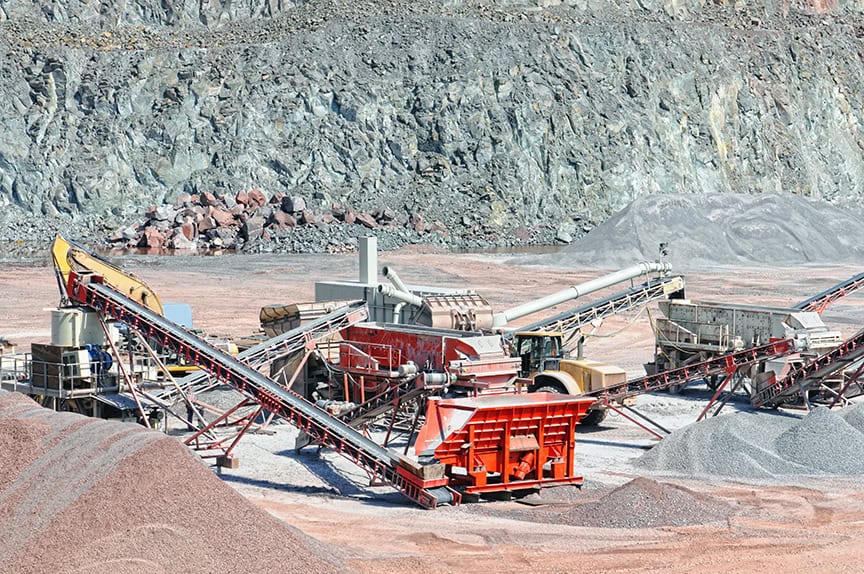
In industries like mining, aggregate, and construction, equipment doesn’t just work hard—it takes a beating. Constant exposure to abrasion and corrosive elements—think of the environment in cement plants—can lead to excessive wear, costly downtime, and frequent repairs. That’s where wear-resistant materials play a crucial role.
Selecting the right wear-resistant material isn’t just about protecting your equipment—it’s also about extending service life, reducing maintenance, and ensuring your operations run efficiently and cost-effectively.
Understanding Wear-Resistant Materials
Wear-resistant materials are engineered to endure punishing, high-friction environments, whether from sliding, scraping, or abrasion. Their purpose is twofold: to reinforce equipment before damage occurs and to simplify repairs (to get you back up and running faster) when wear sets in.
These materials are critical in operations exposed to:
- Abrasion (from dust, sand, or minerals)
- Corrosive environments (chemicals, acids, moisture)
- Extreme temperatures (found in kilns, dryers, and crushers)
Common wear-resistant options include epoxies, ceramics, hardened steels, polyurethanes, and composite materials—and each type comes with different advantages depending on the application.
Explore some of the most popular wear-resistant coatings in our blog, Popular Types of Wear-Resistant Coatings.
Industry-Specific Needs and Considerations
Every industry faces unique wear challenges, so wear-resistant material choice varies across sectors:
Mining
- Constant exposure to abrasive ore, chemicals, and high-speed flow
- Requires resistance to both mechanical wear and chemical attack
Aggregate
- Materials like gravel and crushed stone cause impact and wear from friction
- Durability and corrosion resistance in harsh environments are key
Construction
- Equipment needs to be cost-effective, durable, and easy to maintain
- Must perform in unpredictable outdoor and job site conditions
How to Choose the Right Material
Selecting the right wear-resistant material begins with a detailed understanding of your operating environment. Here are three simple steps to choosing the right wear-resistant material for your industry needs:
1. Assess Your Conditions
- Are you dealing with wet or dry abrasion?
- Is there constant impact or sliding friction?
- What temperatures or chemicals are present?
2. Evaluate Material Properties
- Consider the hardness, toughness, corrosion resistance, and high- or low-impact performance
- How easy is it to apply or repair?
3. Balance Longevity and Cost
- Long-lasting materials may have a higher upfront cost but lower total cost of ownership
- Look for products that minimize downtime and simplify labor needs
Copps Solutions in Action: Armor Plate Wear Compound
At Copps Industries, we’ve formulated a line of Armor Plate Wear Compounds specifically for industries facing extreme wear conditions. One standout product is our Armor Plate Wear Compound – FC-K-038, a two-component, ceramic bead-filled epoxy system built for high abrasion and chemical resistance.
Common Uses:
- Pump casings
- Slurry lines
- Pipe elbows
- Chutes and cyclones
- Coal breakers and pulverizers
Key Advantages:
- Outstanding slide and impact resistance due to bead matrix design
- Broad chemical resistance
- Non-sagging application for vertical and overhead surfaces
- Easy to mix and apply with a fast cure time
- Competitive pricing for cost-effectiveness
- Best for time-sensitive applications where quick curing is critical.
An Example of Customer Success: Fluid Bed Dryer Repair

One of our customers in the frac sand industry, running production 24/7, was struggling with excessive wear on the feed end of their fluid bed dryer.
Previous Fix: Cutting and welding AR plate—time-consuming and labor-intensive
Copps Solution: Applied Armor Plate High Temp Ceramic directly to worn surfaces. The fast-curing epoxy was easy to mix and trowel into place, significantly reducing labor time and getting the equipment back online faster.
Copps Industries: Your Source for Wear-Resistant Solutions
Whether you’re operating in mining, aggregate, or construction, selecting the right wear-resistant material can make or break productivity at your plant or job site. At Copps Industries, we understand the demands you face in extreme environments and offer proven solutions that reduce downtime, extend equipment life, and support efficient maintenance.
Not sure which material is right for your operation? Reach out and we’ll help you find the best solution to meet your wear-resistance needs in any industry.
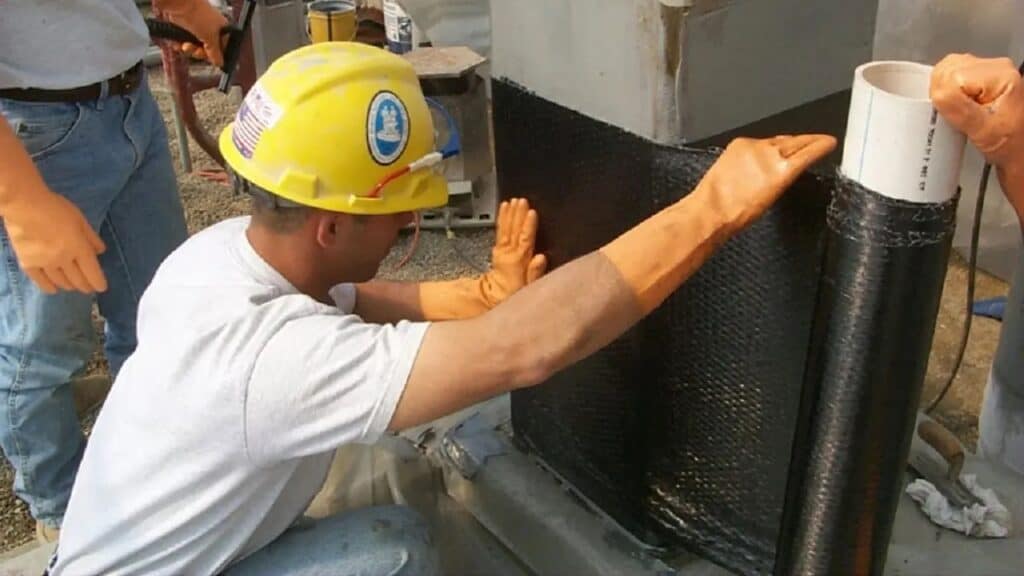
The construction industry is evolving, but when it comes to composites, innovation isn’t just about new materials—it’s also about better applications. While composites have been used in construction for decades, the industry continues to optimize their use for greater durability, efficiency, and sustainability.
Composite solutions like structural reinforcement and pipe repair are helping extend the lifespan of infrastructure, minimize material waste, and improve cost-effectiveness. In this blog, we’re exploring cutting-edge applications and highlighting how composites continue to revolutionize the industry.
Composite Strengthening Systems (CSS)
Aging infrastructure is a growing concern across many industries. Composite Strengthening Systems (CSS) provide efficient and effective solutions for reinforcing and retrofitting aging, damaged, or overloaded concrete, masonry, steel, and timber structures. Instead of costly demolition and reconstruction, CSS extends the lifespan of structures, reduces material waste, and minimizes downtime for businesses and municipalities.
Why Use Composite Strengthening Systems?
Compared to traditional reinforcement methods, CSS offers:
- Structural Reinforcement: Composite strengthening systems deliver significant flexural, axial, or shear strength gains without adding weight or bulk.
- Speed & Ease of Installation: These systems are lightweight and easy to apply, making repairs significantly faster.
- Cost Savings & Minimal Downtime: Composite strengthening systems can often be installed without taking structures out of service, which reduces prep and labor costs and minimizes downtime.
- Real-World Application: Restoring Concrete Pillars Without Disrupting Operations
Many cities and businesses face challenges with aging parking structures, bridge supports, and load-bearing beams. Consider a parking deck experiencing wear and corrosion due to increased vehicle loads. Traditionally, reinforcement would require costly demolition and extensive downtime. Not anymore. Now, crews can use carbon fiber wraps to strengthen critical pillars, allowing the structure to remain open while its integrity is restored
Carbon Fiber Pipe Repair & Manufacturing
Across the globe, millions of miles of pipelines transport water, crude oil, gas, and more. Over time, these critical infrastructures deteriorate due to corrosion, cracking, and manufacturing flaws. Instead of never-ending maintenance and repair, advancements in carbon fiber reduce costs, minimize downtime, and deliver more effective solutions.
Why Use Pipeline Carbon Fiber Wraps?
Carbon fiber is a cutting-edge solution that offers:
- Cost-Effective, Long-Term Repairs: Unlike metal repairs, which are susceptible to rust and degradation, carbon fiber materials offer long-lasting corrosion resistance.
- Cost Savings & Minimal Downtime: Every day a pipeline is down represents a potential loss of $2 million or more in revenue. Carbon fiber repairs allow for faster application and reduced downtime compared to traditional metal replacements.
- Customizable Solutions: Carbon fiber wrap materials can be tailored based on pipe pressure, temperature requirements, and external environmental factors.
Beyond maintenance, carbon fiber has also been integrated into new pipeline manufacturing. Compared to traditional metal piping, carbon fiber offers lighter, stronger, and corrosion-resistant solutions. Each composite pipe is customized based on industry requirements, including:
- High-Temperature Performance (High Tg Materials): High Tg epoxy solutions are capable of withstanding extreme heat without requiring oven curing, allowing for safer, more efficient field repairs.
- Regulatory Compliance: Composites deliver the tailored solutions many industries require to meet safety and performance standards.
Solutions from Copps Industries
Copps Industries provides high-performance structural strengthening solutions that enhance the durability and longevity of critical infrastructure.
Fast Structural Strengthening TB-A-018.B-425
- Best for time-sensitive applications where quick curing is critical.
- Ideal for load-bearing structures that require reinforcement while keeping operations running.
- Works with carbon fiber fabric to provide high-strength adhesion, ensuring long-lasting structural integrity.
Slow Structural Strengthening TB-A-018.B-435
- Designed for applications requiring extended working time, allowing for precise placement and saturation.
- Provides exceptional bond strength and durability, making it a go-to solution for structural repairs.
Tailored Solutions from Copps Industries
- In addition to these off-the-shelf solutions, Copps specializes in custom resin systems designed to meet the unique needs of each customer and your specific industry applications and requirements.
The Long-Term Benefits of Composites in Construction
Beyond delivering speed and ease in specific applications, composites offer long-term advantages that benefit the construction, transportation, and energy industries.
- Reducing Material Waste: Rather than tearing down and rebuilding, composite repairs extend the lifespan of existing structures. Less demolition means lower environmental impact, less downtime, and cost savings.
- Energy Efficiency & Lightweight Construction: Composites are lighter than traditional materials like concrete and steel, lowering transportation and installation costs.
- Improving Safety in the Field: New solvent-free composite solutions reduce hazards for workers, improving overall health and safety conditions on job sites.
Copps Industries: Your Partner in Innovation
While the use of composites in construction isn’t new, their applications continue to evolve and improve efficiency. With composite strengthening systems, advanced pipeline repair solutions, and high-performance epoxy formulations, composites are making construction faster, stronger, and more cost-effective.
The future of construction isn’t about discovering the next material—it’s about taking the materials we have to the next level. At Copps Industries, we provide custom epoxy solutions for nearly any application. For more information about our existing line-up of solutions or tailored formulations, contact us and request a quote.
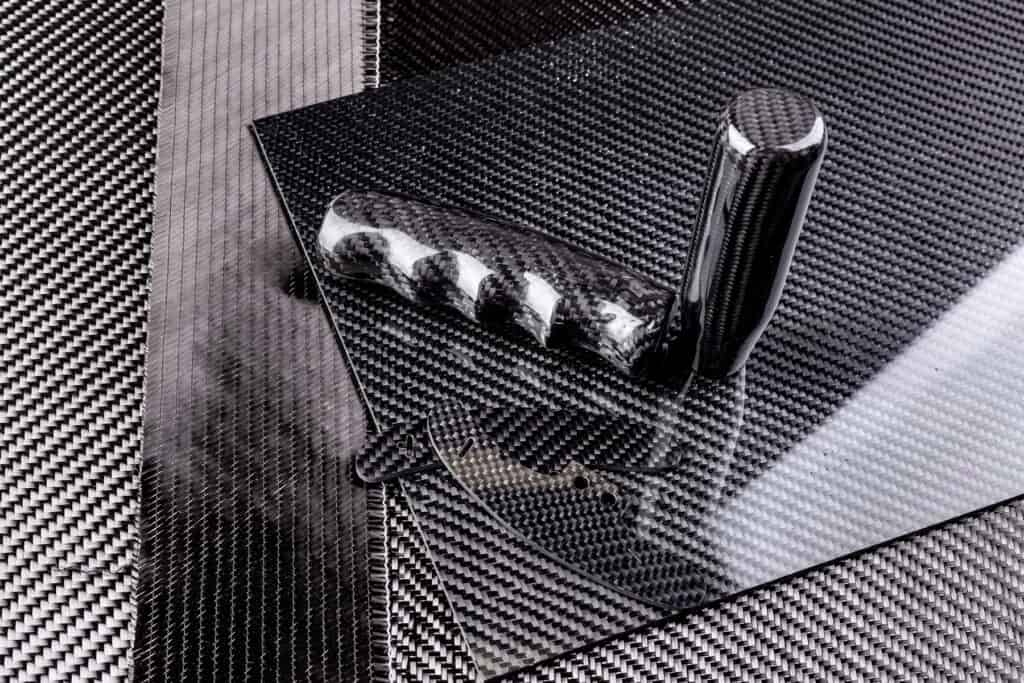
Composites have revolutionized industries from construction and automotive to aerospace and consumer goods. But despite their widespread use, they’re still widely misunderstood. Many assume that composites are just plastics—cheap, weak, or unreliable compared to materials like steel, concrete, and aluminum. But that perception doesn’t align with reality!
In this blog, we’re debunking five common myths about composites to reveal why they’re stronger, more durable, and more versatile than traditional materials.
Myth #1: Composites Are Just Plastic
The Truth: Not all plastics are created equal
It’s easy to assume composites are just another type of plastic, but that’s far from the truth. While some low-grade thermoplastics (like food containers and disposable packaging) are flimsy and heat-sensitive, high-performance composites are designed for maximum durability, strength, and heat resistance.
Consider the attributes of thermoplastics versus thermoset composites:
- Thermoplastics soften when exposed to heat, making them flexible but less structurally sound.
- Thermoset composites, like epoxy-reinforced composites, are rigid, heat-resistant, and capable of withstanding extreme conditions.
These high-performance composite materials are used in aircraft, bridges, wind turbines, and automotive crash structures, proving that composites are far from weak.
Myth #2: Composites Aren’t as Strong as Traditional Materials
The Truth: Composites can be engineered to be stronger, lighter, and more impact-resistant than other materials
A common misconception is that only materials like metal are tough enough to provide the necessary strength for industrial applications. In reality, composites offer a better strength-to-weight ratio than materials like steel, timber, or aluminum.
- Designed Failure Points: Unlike metal, composites can be engineered to absorb impact energy efficiently, making them ideal for crash structures, guardrails, and protective applications.
- Lightweight & High-Strength: Did you know Formula 1 racecars rely on carbon fiber composites to maintain extreme strength without adding weight? Aerospace, automotive, and sports equipment also rely on carbon fiber composites for superior durability and safety without excess weight.
- Reinforcement & Resilience: The use of composites extends even further to applications like reinforcing bridges, parking structures, and pipelines, extending their lifespan and keeping them more resilient than steel or concrete.
Across industries, composites are delivering lighter, stronger, and more resilient solutions than traditionally relied-on materials.
Myth #3: Composites Are Too Expensive to Be Practical
The Truth: The long-term savings outweigh the initial investment
It’s true that composites can have a higher upfront cost than traditional materials, but when you look at the long-term benefits, they’re often more cost-effective.
- Durability & Maintenance Savings: Composites last significantly longer than metal or wood, reducing repair and replacement costs over time.
- Lower Transportation & Installation Costs: Lightweight composites reduce fuel consumption in transportation and make installation easier and cheaper compared to heavier materials.
- Energy Savings in Automotive & Aerospace: Lighter vehicles and aircraft mean less fuel consumption, lower operating costs, and reduced emissions.
For industries where material failure leads to costly downtime—such as pipelines, construction, and aviation—composites offer a more economical solution over time.
Myth #4: Composites Aren’t Environmentally Friendly
The Truth: Composites contribute to sustainability in multiple ways
There’s a misconception that composites aren’t eco-friendly, but actually, they contribute to sustainability across industries.
- Lifespan Extension: Unlike traditional materials that degrade or rust, composites help reduce material waste by extending the lifespan of buildings, infrastructure, and vehicles.
- Lower Carbon Emissions: Lightweight composites improve fuel efficiency in cars, planes, and other methods of shipping and transportation, reducing overall emissions.
- Recyclability & Sustainable Innovation: The composites industry is actively developing more recyclable, biodegradable, and bio-based composite materials, making them an increasingly green choice.
Used strategically, composites can reduce environmental impact by making industries more energy-efficient and less wasteful.
Myth #5: Composites Are Difficult to Work With
The Truth: New advancements are making composite installation, repairs, and manufacturing easier than ever
While some early composites required specialized handling, today’s technological advancements have made them easier to install and maintain.
- Rapid Curing Technologies: High-Tg composites cure at room temperature, eliminating the need for expensive and slow oven curing.
- Field-Ready Solutions: Composite wraps for pipeline repair and structural reinforcement reduce downtime and offer easy application for on-site crews.
- Innovative Manufacturing Processes: Automated production techniques have made composite manufacturing faster, more precise, and more scalable than ever before.
From construction to aerospace, composites are now more accessible and user-friendly, making them a preferred choice for engineers and manufacturers worldwide.
Copps Industries: Setting the Record Straight on Composites
The misconceptions about composites are fading as industries continue to discover their versatility, strength, and sustainability benefits.
- Composites aren’t just plastic—they’re high-performance materials built for extreme durability.
- They’re stronger and more impact-resistant than many traditional materials.
- The long-term savings and durability outweigh the upfront investment in composite materials.
- They play a key role in sustainability, extending the lifespan of structures, reducing emissions, and promoting eco-friendly innovations.
- Advancements in technology have made composites easier than ever to manufacture, install, and repair.
The next time you question whether composites are a viable alternative, remember: Composites are shaping the future of construction, transportation, and beyond. At Copps Industries, we’ve been busting myths about composite epoxy systems since 1979. Reach out to us to learn more about our lineup of solutions and custom-tailored formulations.
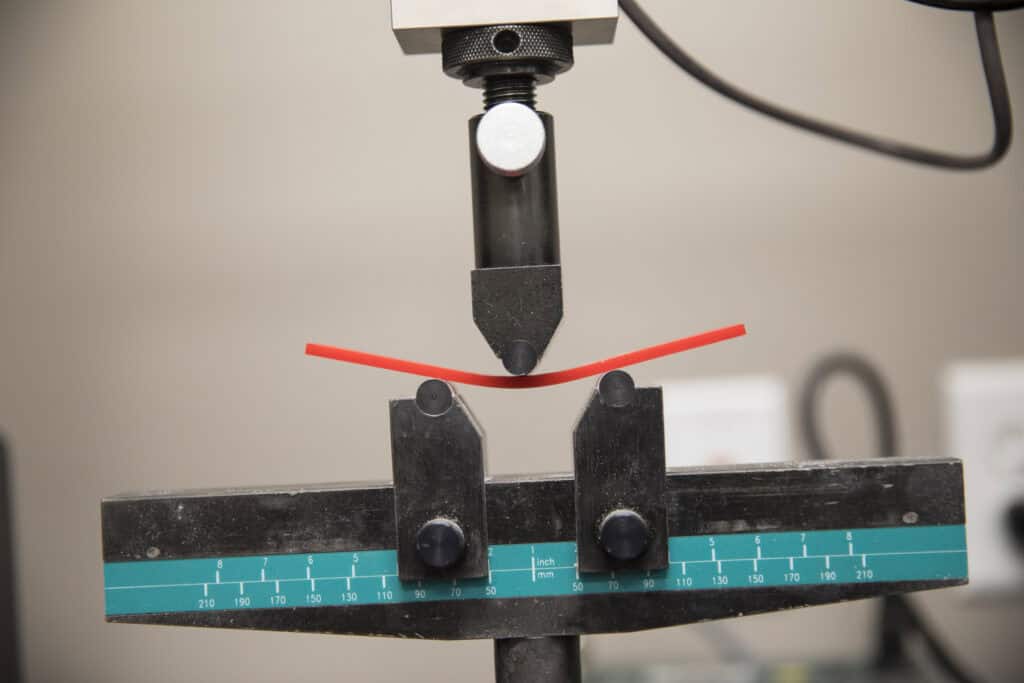
Picture this: Two companies are faced with a critical purchasing decision. One opts for a low-priced product, eager to save on upfront costs, while the other chooses a higher-quality option, recognizing its long-term value.
At first, the low-cost route seems like a smart move. But over time, this company finds itself grappling with frequent breakdowns, higher maintenance expenses, and unexpected downtime. Meanwhile, the second company, willing to spend a little more initially, uncovers reliable performance, fewer disruptions, and steady growth.
This scenario depicts a fundamental truth: prioritizing quality over cost isn’t just a financial choice—it’s a strategic investment in your organization’s success. At Copps Industries, we understand this balance, and we’re committed to delivering high-performance solutions that help your business thrive in the long run.
In this blog, we explore why investing in quality pays off, how to balance cost and performance effectively, and why Copps is your partner for success.
Understanding the Cost vs. Quality Dilemma
When weighing cost against quality, many organizations find themselves at a crossroads. What does “performance” really mean for your operations, and how does it stack up against upfront costs?
Prioritizing cost over performance is a common approach, but it’s laced with misconceptions. Many assume the cheapest option minimizes expenses, which is good for the bottom line in the short term. But overlooking the hidden costs that arise due to increased maintenance, failures, and inefficiencies can hurt your success in the long run. Understanding the real trade-offs is the first step toward smarter decision-making.
The Benefits of High Quality and High Performance
Choosing high-quality, high-performance solutions offers advantages that go beyond the initial purchase price. Reliability, durability, and efficiency ensure smoother operations and significant long-term savings.
Recall the two companies we described earlier. By choosing a higher-quality solution, the second company reduced its maintenance costs and increased its equipment uptime, directly impacting its bottom line. High-performance products don’t just perform better in their intended applications—they enable overall better business performance, too.
The Pitfalls of Picking the Cheapest Option
The allure of low-cost options may be strong, but they often come with big risks. Products chosen solely for their lower price tag may result in:
- Safety hazards
- Higher maintenance costs
- Reduced operational reliability
- Increased downtime
- Shorter lifecycle
- Decreased performance
When making a purchasing decision, it’s smart to consider the total cost of ownership. A low-cost product that fails prematurely (or worse, causes unexpected damage) can end up costing much more in repairs, replacements, and lost productivity than a premium option designed to perform right and last longer.
Why Quality Matters
At Copps, we know quality isn’t just about better performance—it’s about peace of mind. High-quality solutions are reliable, durable, and designed with long-term customer satisfaction in mind. Choosing quality means:
- Less downtime and fewer disruptions
- Long-term cost savings
- Enhanced safety and compliance
- A trusted partnership focused on meeting your unique needs
How to Balance Performance and Cost Effectively
Balancing performance and cost doesn’t have to be an either-or decision. With strategic evaluation, you can maximize the value of your investment while staying within your budget. The most critical things to consider include:
- Total Cost of Ownership (TCO): Factor in all the potential costs of the product, from purchase to disposal.
- Lifecycle Analysis: Assess the product’s durability and longevity.
- Return on Investment (ROI): Measure long-term gains against upfront expenses.
- Risk Mitigation: Measure the likelihood of product failure, downtime, or health and safety issues.
Top 4 Tips for Effective Decision-Making:
We get it—even when you know the high-quality product is the right choice, it can be tough to resist the lower-priced option. For those moments when you’re forced to make a choice, these tips can help you assess your performance requirements against budget constraints:
- Identify your critical needs versus “nice-to-have” features.
- Consider ongoing maintenance costs and the total cost of ownership.
- Align your choices with your long-term operational goals.
- Seek a supplier that offers flexibility and customizable solutions.
Copps’ Approach: Top Quality, Top Performance
Copps Industries doesn’t just deliver products; we deliver performance. Our solutions are rigorously tested to ensure they meet the highest quality standards. And because we’re dedicated to helping your business thrive, we partner closely with you to tailor solutions to your unique needs.
While cost is an important consideration, focusing on long-term value and performance ensures better outcomes for your business. Think of it this way: Investing in quality isn’t an expense—it’s an opportunity.
Ready to learn more about how high-quality solutions pay off? Explore our offerings and request a quote today.
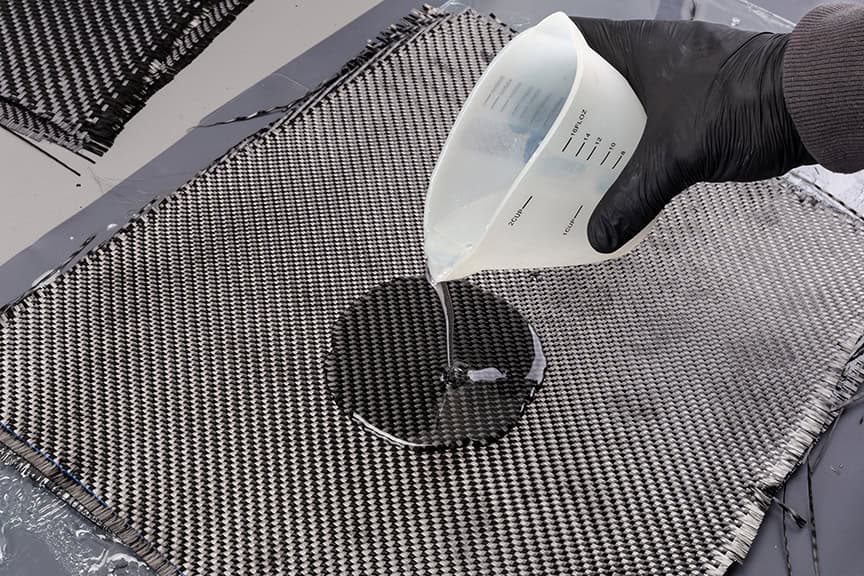
Copps Industries’ composite epoxy systems are engineered to meet unique challenges in high-stakes industries where strength, durability, and adaptability matter. From automotive to marine to aerospace, we develop solutions to elevate performance, drive versatility, and reduce costs.
Copps Industries is committed to developing customizable solutions to meet the exacting demands of diverse industries. Here, we’re exploring the benefits of composite epoxies, from their durability to adaptability, in applications across the board.
Innovation in Composite Epoxy Systems
Composite epoxy systems are revolutionizing how parts and products are designed and manufactured, delivering exceptional strength, versatility, and durability. These compounds empower industries to push performance limits while reducing costs and even environmental impact.
Copps is proud to be at the forefront of innovation in composite epoxies, providing high-quality solutions that meet the evolving needs of nearly every sector. With each stride we make, we’re helping crucial industries become stronger, more resilient, and more sustainable.
Enhanced Performance and Strength
Composite epoxy systems are prized for their ability to deliver strength without adding excessive weight. Copps’ composite epoxy systems withstand high stress and wear, allowing for lighter but stronger components from automotive chassis and aerospace wings.
Our composite epoxy systems deliver high-strength, lightweight performance, which is essential in industries where components need to withstand extreme conditions. In aerospace, they withstand extreme flight stresses. In automotive applications, they replace heavier materials without compromising safety. And in marine applications, components benefit from epoxy solutions that endure harsh conditions, ensuring cost-effective durability.
Versatile Applications Across Industries
Versatility is one of the hallmarks of composite epoxy systems. Copps ‘ composite epoxies excel in varied conditions, from high-strength bonding in aerospace to water and chemical resistance in marine environments.
Composite epoxies can bond with a variety of substrates, offering performance benefits like heat resistance, chemical stability, and insulation. In aerospace, our composite epoxies are engineered to withstand the intense stress and vibration of flight while providing lightweight, high-strength bonds. In automotive applications, our epoxies contribute to the lightweight but durable body panels and chassis to improve efficiency without compromising safety. In marine environments, our epoxies resist chemical exposure and moisture to extend the lifespan of essential parts.
Reduced Costs and Maintenance
In industries where downtime is costly, durability is critical. By engineering systems that excel in severe environments, Copps composite epoxy systems offer long-lasting reliability to improve operational efficiency and reduce maintenance costs.
Composite epoxy solutions need to withstand the test of time through constant exposure and heavy operation. In aerospace, our composite epoxies endure high altitudes and extreme temperatures, allowing essential parts to perform reliably over the long run. For automotive applications, the durability of our epoxies in engine and structural components reduces wear and tear to reduce the need for frequent part replacements. Across marine environments, our composite epoxies withstand constant exposure to harsh conditions, ensuring long-lasting performance with minimal maintenance.
Copps Industries: Performance-Driven Solutions Tailored for Land, Sea, and Air
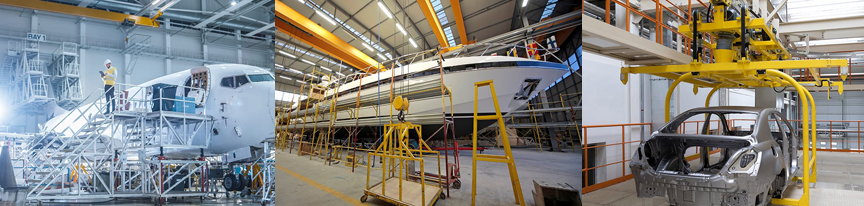
Copps Industries’ composite epoxy systems provide the performance edge you need to excel across any sector. Whether you’re looking for advanced aerospace strength, lightweight automotive durability, or chemical resistance in marine applications, our solutions support your goals.
We’re committed to delivering high-performance composite epoxy systems that empower our customers across land, sea, and air. Reach out to us today to explore how our solutions can support your unique needs and request a quote.
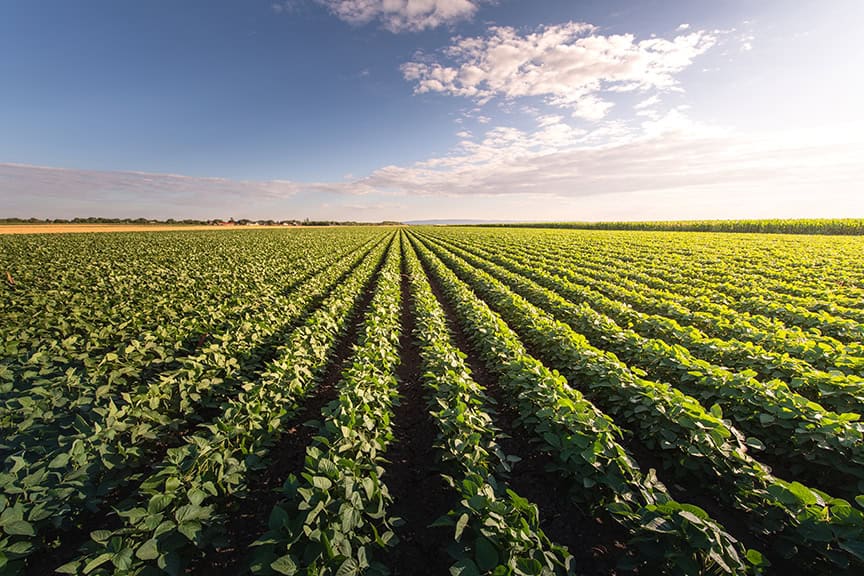
At Copps Industries, we understand that sustainability isn’t just a buzzword—it’s the future of manufacturing. While the demand for bio-based products hasn’t yet taken hold in many markets, we’re staying ahead and preparing for these innovative solutions to someday become indispensable.
The future of bio-based epoxy resins is promising, with the market projected to grow significantly in the coming years. Our forward-thinking approach reflects both our commitment to innovation and our dedication to environmental stewardship. Our exploration of bio-based epoxy products is helping us stay ahead of the curve so we’re ready when the market demands it.
Here’s how Copps is preparing for the shift and why we’re investing in these solutions now.
The Future of Bio-Based Epoxy Products
Bio-based resins, derived from plant-based raw materials rather than traditional petroleum sources, have huge potential across many industries. We predict the popularity and demand will grow significantly in the years to come, especially as regulations and shifting generational values start to shape purchasing decisions. While the U.S. market has yet to embrace bio-based products fully, European customers are already paving the way. Much like their leadership in other environmental efforts, like the Science-Based Targets initiative (SBTi), European industries are exploring bio-based alternatives to address supply chain challenges and create reliable alternatives to oil.
Why Bio-Based Matters
Bio-based epoxy resins are derived from renewable sources like vegetable oils, sugars, and even orange peel. Unlike traditional petroleum-based resins, they:
- Are less toxic and produce fewer volatile organic compound (VOC) emissions.
- Offer environmental benefits by reducing reliance on fossil fuels.
- Can be made degradable, offering a potential solution for end-of-life product disposal.
Bio-based resins are already being used in the automotive, aerospace, and construction industries, where sustainability and performance go hand in hand. As new environmental regulations emerge and more companies focus on reducing their carbon footprints, the demand for bio-based alternatives will likely grow.
Our Work to Stay Ahead of the Curve
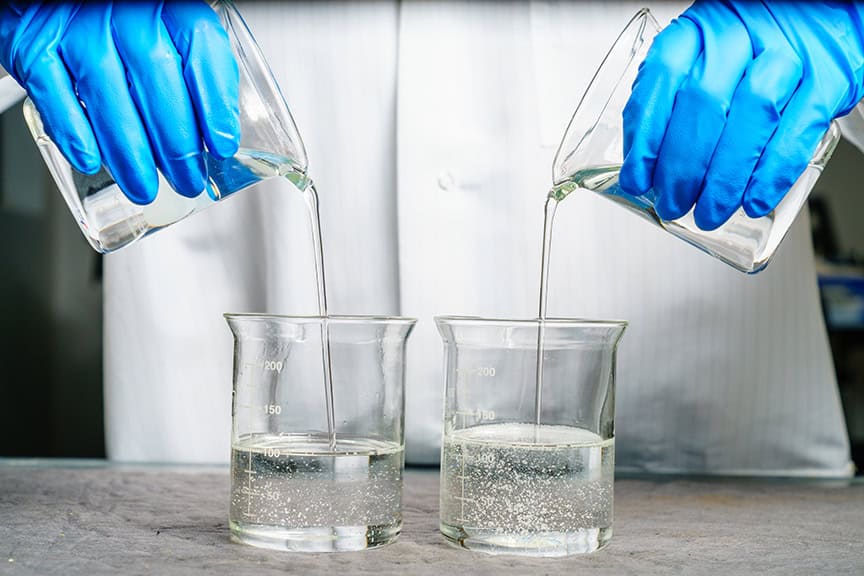
At Copps, we’ve already completed several bio-based formulations. This proactive approach positions us as a leader in the space, ready to bridge the gap between innovation and environmental responsibility.
We constantly ask ourselves, “Is there a safer or better alternative?” and “How can we be as progressive as possible environmentally?” These questions have driven us to explore every angle, from sourcing sustainable raw materials to assessing potential performance trade-offs.
- Sustainability in Sourcing: Bio-based materials rely on agricultural production, meaning infrastructure and supply chains must evolve to scale these solutions. The infrastructure isn’t fully in place today, but we continue to monitor its development.
- Balancing Performance and Cost: Today’s bio-based epoxies are slightly more expensive than traditional formulations, but as adoption increases and infrastructure matures, costs could decrease. We’re ready to help our customers navigate this shift without sacrificing quality or performance.
Market Growth and Opportunities
The bio-based epoxy resin market is projected to reach $4.9 billion by 2032. This anticipated growth is primarily driven by increasing environmental concerns and regulations, but it’s also fueled by advancements in research and development. The next generation of decision-makers, who are sometimes more attuned to environmental concerns, could also accelerate adoption by choosing greener solutions when given the choice.
At Copps, we see bio-based products as a future cornerstone of our industry, and we’re committed to being leaders in this space. Our belief is simple: sustainability and innovation go hand in hand. Even if bio-based products aren’t a significant differentiator today, we’re preparing for when they become essential.
The Copps Commitment: Innovation + Responsibility
As a chemical company, we have a responsibility to lead the way in sustainability. That means thinking about what’s essential today and what’s possible tomorrow.
Our exploration of bio-based epoxy products reflects our dual commitment to innovation and environmental stewardship. We’re committed to both pushing boundaries and considering the long-term impact of our products.
Here’s how we’re leading the way:
- Ongoing Research & Development: We’re investing in research to understand the mechanical properties and chemical resistance of bio-based epoxies and exploring ways to ensure they meet the highest performance standards.
- Learning from Global Trends: Our European customers are already ahead in adopting bio-based solutions, driven by resource constraints and sustainability goals. We’re learning and taking cues from their leadership.
- Listening to the Next Generation: As younger decision-makers enter the industry, they may be more likely to prioritize environmentally friendly options. We’re preparing for this generational shift by developing solutions that meet their expectations.
Looking Ahead
At Copps Industries, we believe in staying ahead of the curve—not just for innovation’s sake but to create a more sustainable future for our customers and the planet. We believe in asking tough questions, exploring safer alternatives, and preparing for the future.
Bio-based products may not yet be mainstream in many industries, but we’re proactively developing formulations and tackling challenges like performance, cost, and scalability. Whether the eventual shift to bio-based solutions comes as a result of customer choice, government mandates, or global trends, Copps will be ready to lead.
Reach out to our team to learn more about the potential of bio-based epoxy products or explore our existing solutions. Together, we can shape a more sustainable future.
Recap: World of Concrete 2025
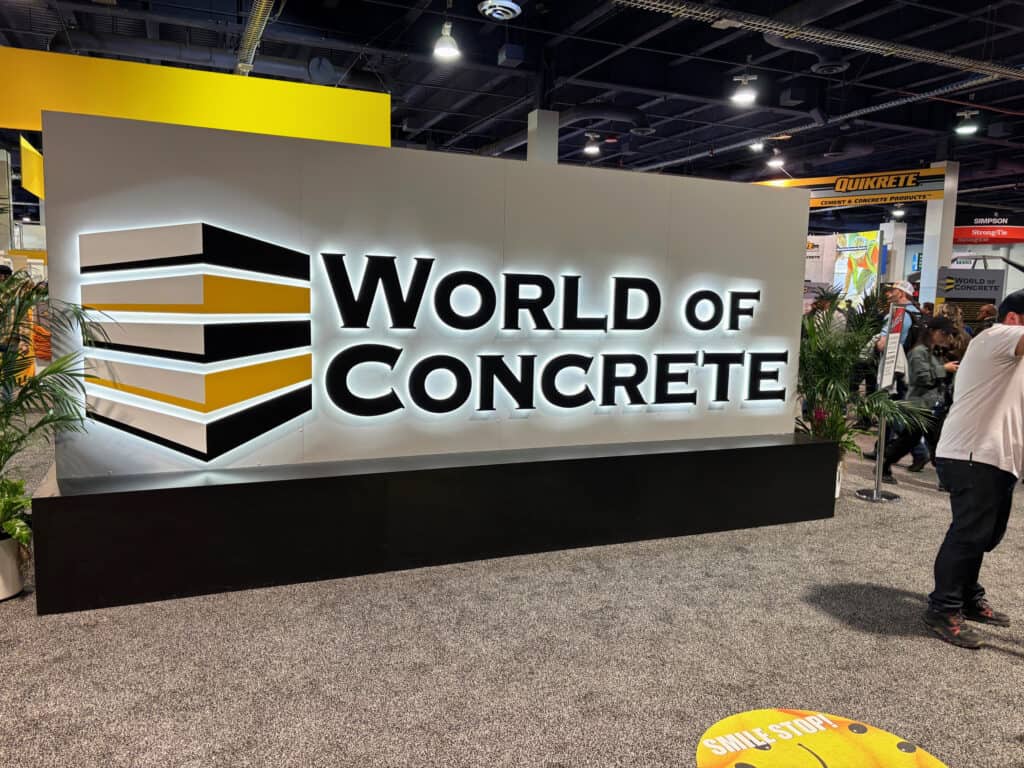
The power players of concrete and masonry came together in Las Vegas for World of Concrete 2025, the industry’s largest and only annual international event dedicated to commercial concrete and masonry construction. Over three action-packed days, professionals from around the world connected to explore cutting-edge technologies and share industry insights.
Held annually by WOC360, World of Concrete features the thrill of indoor and outdoor events, demonstrations, and competitions, showcases innovative products and solutions, and delivers world-class education. It’s the leading event for professionals in concrete and masonry to access insights on the latest products, equipment, and trending topics.
Copps Industries was excited to be a part of the event in Las Vegas on January 21-23. Here, we’re sharing some of the highlights and key takeaways from this year’s show.
Innovation in Concrete & Masonry
Technology and sustainability took center stage, with exhibitors showcasing advancements in concrete admixtures, low-carbon mixes, and state-of-the-art waterproofing solutions. Sessions such as “Meeting & Exceeding Sustainability Targets Using Admixtures and Ensuring Performance of Low Carbon Concrete Mixes” provided critical insights into the trend of reducing embodied carbon in concrete mixtures while maintaining durability and performance.
The Innovative Product Awards celebrated groundbreaking solutions by recognizing manufacturers who are pushing the industry forward with enhanced performance, sustainability, and efficiency.
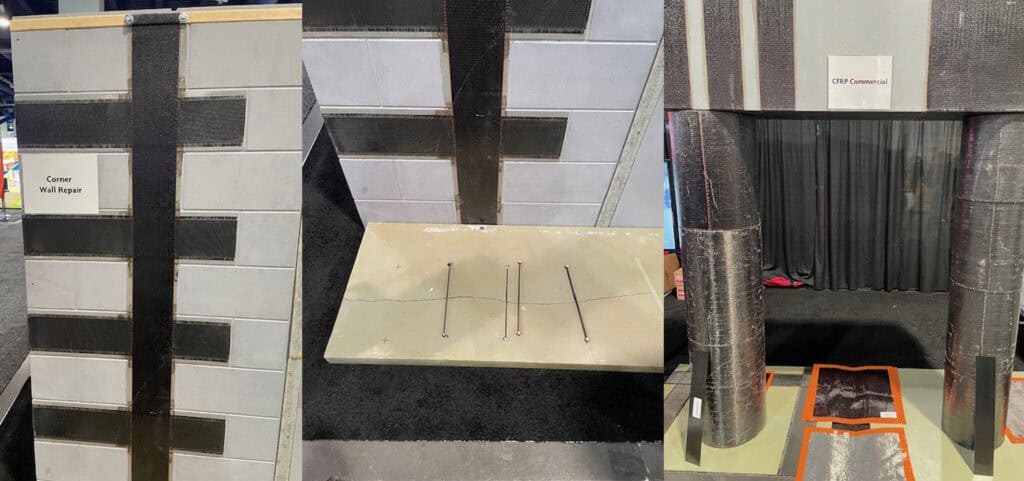
A standout demonstration on the exhibit floor was carbon fiber concrete repair, a game-changing technique that enhances the durability and longevity of concrete structures. Introducing carbon fiber to concrete is an innovative solution for strengthening compromised areas. The lightweight but incredibly strong material is quick to install, low maintenance, and offers greater fatigue resistance compared to other composites.
Showcasing Industry Talent & Skill
The hands-on competitions at World of Concrete are always a highlight, and this year was no exception.
The SPEC MIX BRICKLAYER 500® World Championship, known as the “Super Bowl of Masonry,” saw 27 top bricklayers battle for the title of the 2025 World’s Best Bricklayer. The competition emphasized skill, speed, and stamina, drawing thousands of spectators to witness masonry excellence in action.
MCAA’s Fastest Trowel on the Block featured journeyman masons competing in a high-speed challenge to lay as much of a 30-foot-long wall as possible in just 20 minutes. In the SAIA Scaffold Builders Challenge, crews competed in fast-paced scaffold-building. More than just good fun and craftsman bravado, the competitions emphasized efficiency and safety—both key pillars of successful construction projects.
Advancing Industry Knowledge & Talent
Education is a cornerstone of WOC, and this year’s program offered a range of sessions focused on best practices, emerging technologies, and industry challenges. Highlights included sessions like “Fundamentals & Essentials of Successful Concrete Placement” and “Waterproofing: The Next Generation of Solutions.” WOC 2025 also featured the Weatherton Paper Competition, a platform showcasing students and future industry leaders from the Concrete Industry Management Program.
Connecting to Copps Industries
World of Concrete 2025 highlighted the resilience and collaboration that define the concrete and masonry industry. Engaging with customers and industry partners at WOC 2025 reaffirmed our dedication to delivering high-performance solutions that enhance safety, efficiency, and sustainability. We look forward to applying the insights we gained to our future product development and partnerships.
Missed us at WOC 2025? No problem! Contact us or request a quote to find out how Copps Industries can support your next project.