Category Archive: Uncategorized
Wear-resistant coating materials play a critical role in protecting various surfaces from damage resulting from abrasion, friction, and other forms of wear. By providing an extra layer of defense, these coatings prolong the lifespan of components and reduce maintenance costs. Here, we will dive into the various types of wear-resistant coatings, their unique properties, common applications, and benefits.
Types of Wear-Resistant Coatings
Depending on your needs, there are several types of wear-resistant coatings to choose from:
Hard Chrome Coatings
If an application requires a high level of durability and hardness, hard chrome coatings offer a viable solution. This wear-resistant coating material consists of chromium and is applied using electroplating processes. The resulting surface features superior wear resistance that makes it ideal for many applications, including automotive parts, hydraulic cylinders, and molds.
Thermal Spray Coatings
Thermal spray coatings are available in different materials and offer superior corrosion protection, wear resistance, and thermal insulation. Using processes such as plasma, arc, flame, and high-velocity oxy-fuel (HVOF) spraying, these coatings involve projecting molten or semi-molten particles onto the part’s surface. Thermal spray coatings are used throughout various industries, including oil and gas, power generation, and aerospace.
Ceramic Coatings
Ceramic coating materials like carbides, oxides, and nitrides can protect against wear, chemicals, and heat while enhancing the part’s hardness. These coatings are most commonly applied using processes such as chemical vapor deposition (CVD) or physical vapor deposition (PVD). Due to this coating’s ability to significantly improve wear resistance, it is commonly used for automotive components, cutting tools, and medical implants.
Polymer-Based Coatings
Epoxy, polyurethane, polytetrafluoroethylene (PTFE), and other polymer-based coatings provide high levels of flexibility and wear resistance while minimizing friction. As a result, they are commonly used for applications requiring a high degree of non-stick protection and wear resistance, such as conveyor belts, bearings, and food processing equipment.
DLC (Diamond-like Carbon) Coatings
DLC coatings are composed of thin films of carbon-based materials that feature qualities similar to those of natural diamonds. This type of coating offers exceptional chemical resistance, low friction, and hardness, making them ideal for applications such as automotive components, medical devices, and cutting tools.
Comparison of Wear-Resistant Coatings
When choosing the right wear-resistant coating for your particular needs, there are various factors you should consider. These factors include:
- Wear resistance performance
- Coating thickness
- Adhesion
- Temperature and chemical resistance
- Cost
- Maintenance requirements
- Friction properties
- Surface finish
Each coating type offers its own set of unique strengths and weaknesses. Evaluating the above mentioned properties will make it easier to narrow down your options and make the appropriate selection.
Application-Specific Wear-Resistant Coatings
Wear-resistant coatings are well-suited for various applications throughout a wide range of industries, including:
- Automotive Industry. Coatings are used to protect cylinders, pistons, and engine components.
- Aerospace Industry. Wear-resistant coatings can safeguard landing gear and turbine blades.
- Oil and Gas Industry. This industry relies on wear-resistant coatings to protect pipes, valves, and drilling equipment.
- Manufacturing and Machining Industry. Wear-resistant coatings enhance tool life and reduce downtime for manufacturing and machining equipment.
- Medical and Dental Industry. Wear-resistant coatings are commonly used on dental implants and surgical instruments.
Future Trends and Developments in Wear-resistant Coatings
As coating technologies continue to advance, wear-resistant coatings are becoming more effective and environmentally friendly. More and more types of coating materials are being explored, including nanocomposite coatings with enhanced properties. In addition to new materials and technologies, industries are coming up with innovative coating solutions to address unique challenges, paving the way for enhanced performance and efficiency.
Choose the Right Wear-resistant Coating
There are many different types of wear-resistant coatings, each offering its own unique benefits. Because there are so many options, it’s important to understand their various properties to ensure you make the right selection for your needs. If you need help finding the right wear-resistant coating for your application, Copps Industries is here to help. We offer a wide variety of wear-resistant coating materials and epoxy products to meet your particular needs. For more information about our offerings, contact us or request a quote today.
At Copps Industries, we take our commitment to the environment, our community, and our customers seriously. The Science Based Targets initiative (SBTi) offers companies a clear roadmap for sustainable growth by determining the amount and speed of reducing greenhouse gas emissions. Learn more about how we’re committing to reducing climate change through the Science-Based Targets initiative.
What Are ‘Science-Based Targets’?
Proper organization and project management initiatives can help organizations zero in on social and environmental goals as part of their ESG efforts. ‘Science-based targets,’ in particular, are used to denote the specific goals — and pathways to achieving those goals — that companies will use to curb greenhouse gas (GHG) emissions. The Science-Based Targets initiative (SBTi) is the framework that gives organizations a clear series of steps to future-proof their company’s growth and ensure sufficient reduction in greenhouse gas emissions. Many organizations are starting to focus on these initiatives in order to future-proof their business and develop a pathway to minimizing their organizations’ impact on climate change.
The framework for developing science-based goals is especially helpful in this context. The goals take into account developing scientific knowledge and understanding of greenhouse gases and become very specific, actionable goals. The criteria for determining if a goal is science-based is if it aligns with the scientific evidence of how to achieve the goals in the Paris Agreement, an international treaty focusing on climate change and efforts to curtail or reverse negative environmental changes. The main focus of the Paris Agreement is a hard ceiling on temperature increases — taking measures to ensure the temperature doesn’t increase by 2° C above the known pre-industrial levels — and a softer goal — taking measures to curtail warming so it doesn’t rise by more than 1.5° C.
While many organizations are already motivated to reduce their climate impacts and have made strides in this direction through innovative practices, a clear framework can make those efforts more efficient and effective. Ambitious, scientifically-back goals can also set the groundwork for even more transformation.
Science-Based Targets Initiative Commitment Compliance Policy
The first step in joining the Science-Based Targets initiative is to sign the SBTi Commitment Letter, which allows participants to publicly mark their company as committed to SBTi. If your organization opts to commit to net-zero GHG emission goals or near-term GHG reduction goals, you will have a 24-month timeline to complete these two steps:
- Create a science-based target that fulfills SBTi criteria.
- Submit that goal for SBTi validation. To complete this step, your organization will need to book a target validation slot online and submit the required form.
These two steps are essential for creating science-based targets that align with the core mission of the Paris Agreement and ensuring that your organization is on track to realize your goals.
Copps Industries Science-Base Targets Initiative: Greenhouse Gases and Environmental Commitment
At Copps Industries, we support SBTi and the continued efforts toward a future with reduced or net-zero GHG emissions to slow climate change. Our organization is committed to doing the right thing for all of our stakeholders, including our employees, customers, community, and environment. We continually work toward future-proofing our organization and reducing our environmental impact with initiatives like:
- Removing flammables from our plant
- Replacing chlorinated solvents in favor of more environmentally-friendly compounds
- Removing known and suspected toxic ingredients from our chemical formulations
- Upgrading our packaging to reduce waste
Copps is a leading innovator in the epoxy product space, and our mission is to continually innovate our products and services to meet the needs of our customers and environment. We also prioritize the continued safety of our employees in the workplace through products and processes that have fewer toxins and preserve air quality. We aim to continue focusing on environmental commitment to a cleaner future and providing our clients with consistently high-quality epoxy products.
Learn More About Our Mission
Copps Industries is your go-to partner for high-quality epoxies, but we’re also your partner for environmental action and a more sustainable supply chain. Contact us today to learn more about our initiatives, or request a quote for pricing details on our products.
At Copps Industries, we offer a complete selection of wear-resistant and maintenance epoxy products that protect systems against gradual deterioration and abrasion. Depending on what you require, we can help you find the right product for your system.
We provide a growing product catalog that includes a variety of repair materials, steel filled repair epoxies, alumina ceramic wear-resistant epoxies, industrial concrete joint fillers and floor coatings, adhesives, mill and crusher products, and “DOT” materials.
The following are some of our crusher backing and epoxy maintenance products.
REDBAC Standard Crusher Backing
This product features easy pourability, even consistency, and cured toughness that provide the ideal support for cast wear parts. It also provides superior compressive strength, impact resistance, and service temperature resistance. REDBAC backing does not have Butyl Glycidyl Ether (BGE)1, volatile organic compounds (VOCs), or Nonyl Phenol2.
Copps XP-2000 High Performance Backing
Copps XP-2000 backing helps protect against various types of crushing conditions, including primary crushing, gyratories, wet crushing, and media that is excessively abrasive or hard.
Armor Plate Brushable Ceramic
This ceramic-filled epoxy system is smooth and comprises two components. It yields a low-friction and high-gloss coating that holds up against turbulence, abrasion, and cavitation. It’s suitable for many applications, including lining tanks and chutes, cavitated pumps, butterfly valves, repairing condensers and heat exchangers, repairing cooling pump impellers, and resurfacing pintel housings and rudders.
REDBAC Quick Fill Grout
The REDBAC Quick-Fill Grout epoxy resin system features two components, low viscosity, and 100% solids that work specifically for applications that need vibration control, high strength, and chemical resistance. This epoxy product doesn’t contain Nonyl Phenol2 or Butyl Glycidyl Ether (BGE)1.
Advantages of Epoxy Resin
The benefits of epoxy resin include:
- No VOCs — Our epoxy resin products do not produce volatile organic compound (VOC) fumes that may cause respiratory issues.
- Exceptional Strength — Applications requiring high-strength coatings and maintenance products benefit from our epoxy coatings, which maintain their holding strength and durability even when exposed to other substances.
- Minimal Shrinkage — Epoxy has less than a 1% chance of shrinking, meaning it won’t become loose or weaken after settling properly.
- Adheres to a Variety of Substrates — You can apply our products to many types of substrates—stone, metal, wood, glass, and some plastics—to provide a long-lasting and reliable coating solution.
- Electrically Insulative — Epoxy offers ample insulation to protect electrical components from moisture, dust buildup, and short circuiting.
- Solvent and Chemical Resistance — Epoxy materials protect surfaces from exposure to many types of chemicals and solvents.
- Cost-Effectiveness — Compared to other types of coatings and maintenance products, our solutions are more cost-effective and long-lasting, eliminating the need for additional coatings and repairs in the future.
- Low Toxicity — Our epoxy products are also less toxic than other similar solutions, promoting a healthier environment.
Applications of Epoxy Resin
The applications of our epoxy resins are wide-ranging and can include:
- Epoxy Adhesives — Epoxy resin provides a reliable structural adhesive solution in diverse applications such as snowboards, automobiles, bicycles, and aircraft.
- Artwork — Many artists use epoxy paints for their superior aesthetic finish.
- Industrial Tools — Different types of industrial tools use epoxy resin to protect them against corrosion and wear.
- Electrical Components — Motors, insulators, generators, and transformers often use epoxy resin for insulation and protection against short circuits, dust, and moisture.
- Repair & Maintenance — Consumers frequently use epoxy resin to maintain and repair household items such as china, ceramic, and glass pieces. It can also repair latex, metal, wood, and other synthetic materials.
Why Copps Industries?
The epoxy coatings and maintenance products from Copps Industries offer our customers the solutions they need for a wide range of applications. We have partnered with many businesses over four decades to build custom solutions based on their unique needs. Regardless of your requirements, our combined experience, proven products, and expert staff will meet them.
While many suppliers claim to manufacture dependable wear-resistant coatings and other materials, we are among the few that offer practical solutions that help address real-world problems. As a private label manufacturer and leader in custom formulations, Copps Industries is a trusted provider of wear-resistant epoxy and epoxy repair products for the world’s leading OEMs.
Learn more about our products by reviewing our list of wear-resistant coating and maintenance products, or request a quote to get started on a custom solution.
Epoxy resin systems typically comprise of two main parts: a Part A resin and a Part B hardener. These two parts need to have the right ratio for the system to work properly. Typically, a chemist will calculate this ratio chemically to ensure a well-balanced system. With the right ratio of resin to hardener, the chemically reactive portions of the epoxy resin system will link together and cure into a strong, high-quality end product.
Other kinds of non-epoxy polymers will allow for different levels of hardener to either reduce or extend gel time. However, this isn’t the case with epoxy resin systems they require specific ratios. If you add too much hardener to an epoxy resin system, it will decelerate the curing process, leading to an improperly hardened and non-functioning product. This makes it crucial to have the right ratio of resin to hardener if you want to create an epoxy system that truly works.
Why You Should NOT Vary the Ratio
Varying the required ratio of Part A to Part B to any degree will compromise the integrity of the epoxy system, forming a weak product that performs poorly.
Epoxy systems come in different cure rates depending on the process’s specific temperature. Generally, applications with cooler environments will use a system that cures faster, while hotter environments typically implement a slow curing system. The ideal temperature range for epoxy systems normally falls between 65° F and 80° F, or 18° C and 26° C.
Before using the epoxy system for the first time, it’s often best to produce a small batch for testing to gauge how the mixing and curing process works. Doing so is a potentially critical step to take if you want to avoid expensive mistakes and inadequate cures. This is particularly the case when working with new products, working in environments with different temperatures, or if it’s your first time going through the epoxy mixing process.
Epoxy Resin Formulas
The combination of polymerization processes and chemical compounds of the epoxy resin system will influence the resulting characteristics of the formula. There are many types of formulas you may use depending on the desired characteristics.
The following are some of the core properties of epoxy resin formulas:
- Chemical stability
- Strong adhesive bond
- Corrosion resistance
- Heat resistance
- Minimal moisture absorption
- Reduced shrinkage after curing
- Electrical insulation
- Excellent fatigue and flexural strength
- Absence of volatile organic compounds (VOCs)
Learn More
The manufacturer of the epoxy resin should include instructions disclosing the ideal resin-to-hardener ratio. When mixing the epoxy, this ratio ensures an effective epoxy system that cures properly with optimal strength and performance.
If you’re searching for the best epoxy resin solutions for your application, Copps Industries offers a selection of top-quality products. As a leading supplier of epoxy resins, we carry more than 500 epoxy products and have over 400 international customers. We understand the importance of having the right ratio for each product and can advise you on product development.
For more information about resin to hardener rations, or to get started on you epoxy resin solution, request a quote today.
Although many people use the terms polyurethane and epoxy interchangeably, they are actually two distinct types of coating with their own properties and advantages. As they are both hardwearing resin systems, each one functions well in busy plants or other facilities where physical impacts are common. However, with such a wide range of polyurethane and epoxy options to choose from, it may be challenging to find the best option for a given application. By understanding the differences between each one, you’ll easily be able to make a decision.
Epoxy Coatings
A major advantage of epoxies is their surface tolerance, as they can adhere extremely well to a variety of substrates. Depending on the intended application, manufacturers may choose any one of a number of epoxy options, each with its own specific properties. For example, an epoxy may be chemical resistant or fast setting.
Regardless of the specific epoxy, in general, this type of coating offers impressive amounts of durability and impact resistance, making it an ideal choice for either a primer/intermediate coat or a topcoat. Epoxies also offer the following significant benefits:
- Ability to Bond To Concrete: In situations where a concrete substrate must receive a coating, epoxies can bind with it both chemically and mechanically.
- Thick Build Coats: Thanks to their thickness, epoxy build coats are able to be self-level, and can create smooth surfaces by filling cracks and other small blemishes.
- Long Term Durability and High Performance: Once treated with an epoxy resin, substrates will have a harder, more durable surface that provides good impact resistance.
Polyurethane Coatings
While epoxy coatings are hard and offer high amounts of impact resistance, polyurethane provides a softer option. It is more scratch-resistant and ideal for flexible substrates. Polyurethane’s flexibility also helps prevent concrete cracks from moving through the coating. Polyurethane has numerous advantages despite its thinner build coats, including:
- UV Resistance
- Impact and Abrasion Resistance
- Gloss Retention
- Color Stability
Polyurethane vs. Epoxy
Polyurethane and epoxy are both advantageous coating solutions, but they differ from one another in several key ways. First, these two types of coatings are different in cost. Polyurethanes will typically cost more than epoxy. In certain applications, polyurethane can be a more cost-effective solution.
Additionally, these two types of coatings offer benefits that serve different types of substrate. Epoxy offers higher levels of rigidity and adhesion than polyurethane, making it better suited for harder surfaces. In particular, manufacturers will often favor epoxies for the priming of concrete. Polyurethane, on the other hand, provides enhanced cosmetic performance characteristics that offer holistic protection for the entire system.
Industrial Epoxy Solutions From Copps Industries
For applications that require significant amounts of durability and high performance, epoxy resins are the ideal choice. Since 1979, Copps Industries has been dedicated to providing the finest industrial epoxies in the field. Throughout our decades of experience, we have successfully diversified our lineup to offer upwards of 500 products in 27 different countries. Markets we serve include:
- Electronics
- Civil Engineering
- Structural Adhesives
- Aggregate/Mining
We are dedicated to continually manufacturing products of the highest caliber at our ISO 9001:2015-certified facilities. Contact us or request your quote today to learn more about our epoxy resin solutions.
As a way of adding protection and gloss to items, Diamond Clear Epoxy are widely used for bars, tabletops, river tables, jewelry, and much more. Epoxy resins are a popular product used for various applications. However, determining the best type of epoxy for your project can be difficult.
Two common types of epoxies are table top epoxies and casting epoxies. While the two are very similar, they each have their unique properties and ideal uses. Regardless of the epoxy needed for your project, be sure to read and follow the manufacturer’s instructions because mistakes can have a huge impact on the final product.
Table Top Epoxy vs. Casting Epoxy
Two of the most popular Diamond Clear Epoxy are table top epoxy and casting epoxy. These two share similarities, but they are very different to work with and are meant for different applications.
Table Top Epoxy
As the name implies, table top epoxy is best for pouring over flat surfaces, such as table tops, bars, counters, or resin art. It is a self-leveling epoxy meant for thin pours in thicknesses of usually 1/4’’ or less. Pour thicknesses vary depending on the application, but it is important to note that using table top epoxy for embedding thick objects takes several applications and hours.
With table top epoxy’s recommended 1:1 mixture, it is ideal for use by both beginners and professionals. The main advantages of table top epoxy over casting epoxy are its higher viscosity and faster cure time of 12-24 hours.
Casting Epoxy
Also referred to as deep pour resin, casting epoxy is used for thick pours of up to 2’’. Casting epoxy is commonly used for river tables, embedding and encasing objects, jewelry, and more. It offers a lower viscosity than table top epoxy and a slower cure rate of 24-36 hours.
The longer cure time for casting epoxy allows for a longer working time, but care must be taken to prevent dust and debris from settling into the resin. The typical mixture for casting epoxies is 2:1, although some manufacturers have variations with a 1:1 or 3:1 ratio.
Advantages of Diamond Clear Epoxy
There are several features of Diamond Clear Epoxy epoxies that make them ideal for many applications. Advantages of using Diamond Clear Epoxy in your project include:
Click to Expand
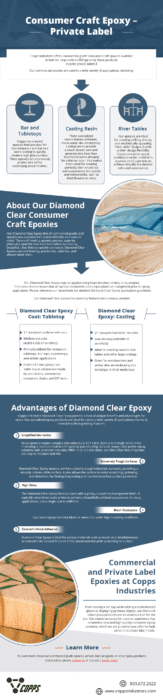
- Blush Resistant. Even in high humidity conditions, Diamond Clear Epoxy does not blush or sweat.
- High Gloss. The formula for Diamond Clear Epoxy cures with a highly glossy and transparent finish. To achieve this polished appearance, it typically takes only three coats or less.
- Simplified Mix Ratios. Simple mix ratios make using Diamond Clear Epoxy easier to measure and mix. This makes it preferred by many as it reduces the risk of minor errors that affect the final product.
- Tough Surfaces. Diamond Clear Epoxy are formulated to tough industrial standards, providing indestructible surfaces for your project. Epoxy results in long-lasting, maintenance-free surface protection that resists scratching, yellowing, and distortion.
- Wood Adhesion. Diamond Clear Epoxy are the ideal solution for porous materials, helping protect the surface while accentuating the wood’s natural features.
Copps Industries’ Diamond Clear Epoxy
At Copps Industries, we offer an Diamond Clear Epoxy line made for your unique applications, from sealing a bar top to adding a gleam to objects. With our high-quality consumer epoxy products, we can meet your bulk order or private label needs.
The two primary varieties of Diamond Clear Epoxy we feature are Diamond Clear Epoxy Coat Table Top Epoxy and Diamond Clear Epoxy Casting Epoxy. Our commercial-grade craft epoxies are self-leveling and create beautiful and clear finishes quickly and easily with superior physical properties. You can apply our Diamond Clear Epoxy using foam brushes, rollers, or squeegees.
From comprehensive sales and customer service to product development and technical support, Copps Industries is here to provide the best solutions for our customers. To learn more about our line of Diamond Clear Epoxy, or to get started on your epoxy solution, contact us or request a quote today.
Epoxy resins adhere and cure on hard surfaces, providing a versatile polymer adhesive. Beyond their temperature-resistance capabilities, high-temperate epoxies feature many favorable qualities, including resistances to moisture, chemicals, impact, and corrosion.
High-temperature epoxies maintain their properties even when exposed to extreme temperatures. Harsh industrial environments rely on high-temperature epoxy coatings over other adhesive types because of the improved heat resistance and durability they provide in severe operating conditions. This blog post will discuss the versatile nature of high-temperature epoxies and their uses across various industries.
What is High-Temperature Epoxy?
For many applications, finding an appropriate high-temperature adhesive is vital for the success of the project. Manufacturers working in challenging environments often opt for a high-temperature epoxy resin, a specially formulated product that withstands temperatures up to 450°F and cures even in high-heat conditions. Other advantageous qualities of high-temperature epoxies include:
- Durability
- High abrasion resistance
- Good clarity
- Low viscosity
- Thermal conductivity
- Dimensional stability at high temperatures
These epoxy resins offer exceptional wetting characteristics when used in conjunction with aramid or carbon fiber. They display high degrees of chemical resistance and withstand steam exposure. Additionally, high-temperature epoxies are an ideal choice for encapsulation and potting, thanks to their thermal conductivity.
When the time comes to choose the appropriate adhesive for a project, it is essential to account for the expected operating temperature and the requirements for the product’s ultimate performance properties. Other vital considerations include:
- Duration of exposure to high temperatures
- The glass transition temperature of an adhesive
- Coefficient of thermal expansion and bonded substrates
High-Temperature Epoxy Applications
The versatility of high-temperature epoxies makes them ideal for use in a wide range of industries, such as:
- Construction
- Adhesives
- Coatings
- Composites
- Electronics
They also provide excellent adhesion to many materials, including:
- Plastics
- Ceramics
- Metals
- Glass
High-temperature epoxies feature a versatile range of capabilities. Examples include:
- Creating ultra-thin bond lines
- Superior protection and performance when bonding/coating electronic components
- Protecting and sealing porous materials
- Wet-lay laminating and vacuum-bagging of composite parts
- RIM tooling and vacuum forming
- Bonding and encapsulation
Our High-Temperature Epoxy
As one of the industry’s leading providers of high-caliber, sustainable epoxies, Copps Industries designs and manufactures high-temperature epoxy resins suitable for use in various unique environments. We work closely with our customers to find the ideal solution for their application, improving results while reducing costs.
Our product line contains two epoxy resins specifically designed for high-temperature use.
High-Temperature Ceramic Wear Compound K-037
Our High-Temperature Ceramic Wear Compound K-037 system is suitable for environments with temperatures up to 450°F. This ceramic-bead-filled, two-component epoxy system features strength, corrosion resistance, and abrasion resistance in severe service conditions.
REDBAC XTra Temp High-Performance Grout K-052
This epoxy system provides significant strength and chemical resistance, making it ideal for applications involving corrosive compounds. The REDBAC XTra Temp High-Performance Grout K-052 system maintains performance in temperatures up to 400°F. It can handle a wide range of challenging tasks, such as protecting concrete surfaces, grouting machine bases, and repairing damaged foundations.
High-Temperature Epoxy Solutions From Copps Industries
For over 40 years, Copps Industries has been designing high-quality, heat-resistant epoxy resins. With over 400 clients in industries ranging from electronics to civil engineering, our diverse product line contains solutions to meet any customer’s unique needs. We are ISO 9001:2015-certified and dedicated to producing sustainable and reliable resin solutions.
To see how our high-temperature epoxy resins can improve your high-heat application, please contact us or request your quote today.
Epoxy resin has many industrial applications and possesses greater thermal and chemical resistance – as well as strengthened mechanical properties – than other types of resin. When in liquid form, epoxy resin is poured into a mold or painted over a material in layers to create a protective outer coating. After curing, the material hardens into a solid and becomes durable and structurally stable. This combination of features makes epoxy resin extremely useful in a number of applications, from industrial tooling to art projects and automotive manufacturing
The specific combination of chemical compounds and polymerization processes will impact the resulting core characteristics of an epoxy resin formula.
Here are some of the trademark properties of epoxy resin formulas:
- Heat-resistance
- Chemical stability
- Electrical insulation
- Low moisture absorption
- Durable adhesive bond
- Anti-corrosive
- Excellent fatigue strength and flexural strength
- Low shrinkage after curing
- Absence of VOCs (volatile organic compounds)
To begin the application process the epoxy resin is mixed with a co-reactant, also called a hardener, which typically comes in a separate compartment of the same package. The chemical reaction begins as soon as the two chemicals are mixed and depending on the formulation can become solid very quickly or slowly depending on your requirements. The epoxy resin manufacturer should provide instructions about the ratio of epoxy to hardener that should be used to achieve maximum strength and performance.
What’s the Difference Between Casting and Coating Epoxy Resins?
Casting and coating epoxy resins are unique but related compounds. Choosing between the two will ultimately determine how the finished product will look and function.
Casting resins, also called “deep-pour resin” or “pouring plastic,” are used for clear encasings and suspensions. The user pours the material into a mold and then cures it to retain the same shape. Casting resins are commonly used to create crafts, jewelry, sculptures, and memorabilia. Manufacturers can also produce aggregate, molded plastics, or electrical insulation with casting resin. Engineers design automotive parts, aerospace devices, sports equipment, and hundreds of other products with compounds that are fortified with epoxy resin.
Coating resins, on the other hand, are aptly named: they are used to coat materials, such as metal, concrete, or wood, to make them stronger, chip-resistant, easier to clean, water-resistant, and rust-proof. A thin layer of coating resin can also glue materials together or preserve paper. In the electrical manufacturing sector, coating resins are applied to overmold circuits and transistors, which holds components together and protects against corrosion.
Beyond these differences in application, there are a few other notable distinctions between casting and coating epoxy resin:
(Click to Expand)
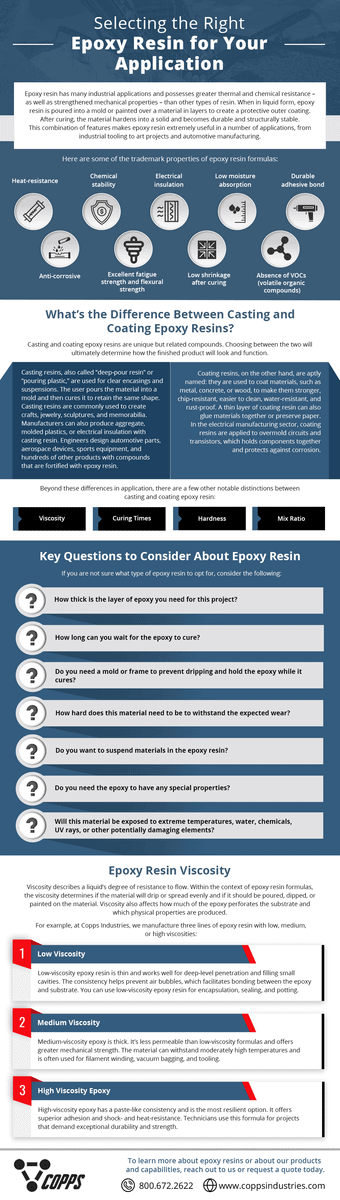
- Viscosity: Casting resins are normally thinner compared to coating resin.
- Curing Times: Because liquid casting resin is poured into thick layers, they take longer to cure to avoid shrinkage and heat build up..
- Hardness: Coating resins are usually stiffer and harder than casting resins.
- Mix Ratio: Most coating resins use a 1:1 ratio, but casting resin formulas can vary, such as 1:1 or 2:1.
Even though there are significant similarities between the two formula types, it’s usually easier to use the formula that’s best suited to your intended application.
If you pour casting resin on a surface instead of using a thin layer of coating resin, for example, the resin will run off the edges and will be very slow to harden.
Alternatively, if you pour coating epoxy into a mold, you’ll need to pour multiple thin layers and wait for the material to cure between applications. Otherwise, the heat generated from the material poured in a large mass will accelerate the chemical reaction and cause yellowing or cracking.
Key Questions to Consider About Epoxy Resin
If you are not sure what type of epoxy resin to opt for, consider the following:
- How thick is the layer of epoxy you need for this project?
- How long can you wait for the epoxy to cure?
- Do you need a mold or frame to prevent dripping and hold the epoxy while it cures?
- How hard does this material need to be to withstand the expected wear?
- Do you want to suspend materials in the epoxy resin?
- Do you need the epoxy to have any special properties?
- Will this material be exposed to extreme temperatures, water, chemicals, UV rays, or other potentially damaging elements?
Epoxy resin systems can be tailor-made to suit unique project needs. Manufacturers use a variety of co-reactants, including, for example, polyfunctional amines, phenols, and alcohols all of which produce slightly different results. The type of base epoxy and additives in the formula can also change the resin’s viscosity and intrinsic properties.
Epoxy Resin Viscosity
Viscosity describes a liquid’s degree of resistance to flow. Within the context of epoxy resin formulas, the viscosity determines if the material will drip or spread evenly and if it should be poured, dipped, or painted on the material. Viscosity also affects how much of the epoxy perforates the substrate and which physical properties are produced.
For example, at Copps Industries, we manufacture three lines of epoxy resin with low, medium, or high viscosities:
- Low Viscosity
Low-viscosity epoxy resin is thin and works well for deep-level penetration and filling small cavities. The consistency helps prevent air bubbles, which facilitates bonding between the epoxy and substrate. You can use low-viscosity epoxy resin for encapsulation, sealing, and potting.
- Medium Viscosity
Medium-viscosity epoxy is thick. It’s less permeable than low-viscosity formulas and offers greater mechanical strength. The material can withstand moderately high temperatures and is often used for filament winding, vacuum bagging, and tooling.
- High Viscosity Epoxy
High-viscosity epoxy has a paste-like consistency and is the most resilient option. It offers superior adhesion and shock- and heat-resistance. Technicians use this formula for projects that demand exceptional durability and strength.
Epoxy Resin Solutions at Copps Industries
Copps Industries has been a leading provider of quality epoxy resin solutions for over four decades. Our formulations are thoroughly tested for quality assurance and have demonstrated practical applications in a broad range of industries. To learn more about epoxy resins or about our products and capabilities, reach out to us or request a quote today.
High-quality epoxy grouting solutions are critical for the secure installation and stabilization of on and offshore oil and gas exploratory equipment and structures. There are a wide range of epoxy grouts available that exceed the bond strength, chemical resistance, and alignment performance of more traditional cementitious grouts.
In this blog, we’ll cover the basics of epoxy grout, suitable applications, and selection considerations for the oil and gas industry.
What is Epoxy Grout?
The most simplified definition of epoxy grout is epoxy grout fills the void between steel and concrete in a structure or machinery mount to provide stabilization.
Epoxy grout has become an increasingly popular option for many applications. Epoxy grout is made from a two-part system containing an epoxy resin and a hardener with an engineered aggregate added to meet the desired specifications. Epoxy grout solutions offer several advantages over cement-based grouts.
Unlike cementitious grout, epoxy grout is non-porous, which makes it waterproof and highly resistant to stains, mildew, and mold. When cured, epoxy grout is extremely hard and durable. It can be formulated to withstand exposure to harsh chemicals without the need for a sealer, making it ideal for many industrial and commercial applications.
Compatible Oil & Gas Applications
Offshore oil and gas structures are designed with foundations that withstand the full forces of nature, including powerful ocean conditions.
Offshore structures are typically constructed with piled and grouted foundations. Pilings are driven through the legs of the structure and into the seabed, leaving a void between the piling and leg. The void is filled with grout, displacing the water. Once cured, the grout bonds the piling and leg together, resulting in a structure able to withstand the power of the ocean. The characteristics of epoxy grout make it an ideal choice for offshore applications.
Epoxy grout is also commonly used to mount and anchor heavy machinery and provide a secure and stable work surface for the equipment. Unlike traditional cement grout which may crack from vibrational impact, epoxy grout dissipates vibrations, ensuring that proper load transfer between the base and sole plate is maintained
Epoxy grout is also used to mount the sole plates that attach heavy equipment and machinery to the floor. Epoxy grout between these layers helps to transfer load forces while keeping the plates aligned, level, and stable. When properly installed, epoxy grout provides superior performance able to withstand heat, harsh chemicals, and stress better than cementitious grout.
Download Our eBook
Epoxy grouts are able to meet the stringent structural demands of onshore and offshore oil & gas equipment by providing superior bond strength, alignment performance, and chemical resistance relative to traditional cementitious grouts. Our eBook, A Complete Guide to Oil and Gas Epoxy Grouting Solutions, provides a comprehensive overview of epoxy grouts for oil & gas applications.
Learn More >
How to Choose an Oil & Gas Epoxy Grout
When choosing an epoxy grout for oil and gas applications, it is essential to select a type specially formulated with the following features:
- Extreme environmental condition resistances, such as very high and very low temperatures
- Fatigue resistance
- Chemical resistance
- Non-corrosiveness
Epoxy grout with these features will ensure long-lasting security, stability, and alignment.
At Copps Industries, we have several epoxy grout solutions formulated for common conditions encountered in oil and gas applications. For example:
- X-TRA Temp High Performance Grout (K-052) is formulated for extreme high-temperature applications that require chemical resistance and durability. X-TRA Temp High Performance Grout has a service temperature of as high as 425° F with a very low mixed viscosity of 7,000 cP.
- Low Temperature (K-026) is designed for cold weather applications, and allows for pouring in air temperatures between 25° F and 60° F, with a mixed viscosity of 20,000 cP at 40° F. Low Temperature (K-026) is an ideal grout for use in cold climates where outdoor pours are required.
An experienced manufacturer and distributor can assist you in selecting the most appropriate epoxy grout solution for your specific application. When sourcing epoxy grout for your project, ensure that you choose a provider who has an ISO 9001:2015 certification. Adherence to this standard ensures a product that was created under strict quality assurance procedures.
Oil & Gas Epoxy Grout Solutions at Copps Industries
At Copps Industries, we are committed to providing our clients with unparalleled service and the highest quality products available. We are an ISO 9001:2015 certified manufacturer and supplier of industrial-grade epoxy, offering a wide range of unique and proven formulated systems. We have been using innovative practices and cutting-edge technology to develop solutions that address complex challenges within a variety of industries since 1979.
To learn more about epoxy grout solutions for oil and gas applications, please reach out to us today.